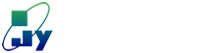
Fluorine rubber refers to a synthetic polymer elastomer containing fluorine atoms on the carbon atoms of the main chain or side chain. It not only has good mechanical properties, but also has high resistance to high temperature, oil and various chemicals. Its characteristics and comprehensive performance are particularly excellent, so it has a wide range of applications, especially in the production of special sealing products. It is an indispensable material in modern aviation, missiles, rockets, aerospace and other science and technology and other industries (such as automobiles) .
1. Structural characteristics and application fields of fluororubber
Because there is no unsaturated C=C bond structure in the main chain of polyolefin fluororubber (type 26 fluororubber, type 23 fluororubber) and nitroso fluororubber. Reduces the possibility of degradation and chain scission on the main chain due to oxidation and pyrolysis. The methylene group in vinylidene fluoride plays a very important role in the flexibility of the polymer chain. For example, fluorine rubber 23-21 and fluorine rubber 23-11 are composed of vinylidene fluoride and chlorotrifluoroethylene in a ratio of 7:3 respectively. And the ratio of 5:5, obviously, the former is softer than the latter.
Whether it is vinylidene fluoride and chlorotrifluoroethylene, or the copolymers of the former and hexafluoropropylene, and their terpolymers with tetrafluoroethylene, they can be mainly crystalline or amorphous. This depends on how much of one monomer is involved when the other monomer is the main chain segment of the copolymer. Electron diffraction studies indicate that when the mole fraction of hexafluoropropylene in the vinylidene fluoride segment reaches 7%, or the mole fraction of vinylidene fluoride in the chlorotrifluoroethylene segment reaches 16%, the two copolymers still have and Its crystal structure is comparable to that of a homopolymer. However, when the mole fraction of hexafluoropropylene in the former increases to more than 15%, or the mole fraction of vinylidene fluoride in the latter increases to more than 25%, the crystal lattice is greatly destroyed, causing them to have an amorphous shape with mainly rubber properties. structure. This is due to the increase in the amount of the second monomer introduced, which destroys the regularity of its original molecular chain. Fluorine rubber can be used together with nitrile rubber, acrylic rubber, ethylene-propylene rubber, silicone rubber, fluorosilicone rubber, etc. to reduce costs and improve physical and mechanical properties and process performance.
The earliest fluorine rubber was poly-2-fluoro-1,3-butadiene and its copolymer with styrene, propylene, etc., which was trial-produced by DuPont Company in the United States in 1948. Its performance is no better than that of chloroprene rubber and butadiene rubber. , and it is expensive and has no actual industrial value. In the late 1950s, the American Thiokol Company developed a binary nitroso fluororubber with good low-temperature performance and resistance to strong oxidants (N2O4). Fluorine rubber began to enter practical industrial applications. China has also developed a variety of fluororubbers since 1958, mainly polyolefin fluororubbers, such as type 23, 26, 246 and nitroso fluororubber; later, a newer variety of tetrapropylene fluororubber was developed , perfluoroether rubber, fluorophosphorus rubber. These fluorine rubber varieties are first based on the supporting needs of aviation, aerospace and other national defense and military industries, and are gradually promoted and applied to the civil industry sector. They have been used in modern aviation, missiles, rockets, aerospace navigation, ships, atomic energy and other technologies as well as automobiles, shipbuilding, chemistry, Petroleum, telecommunications, instruments, machinery and other industrial fields.
Fluorine rubber is widely used in daily life, such as automotive parts, aviation and aerospace fields, mechanical seals, pumps, reactors, agitators, compressor casings, valves, various instruments and other equipment as valve seats. , valve stem packing, diaphragms and gaskets, as well as in the rubber sheet industry, semiconductor manufacturing industry and food and pharmaceutical industries.
With the use of unleaded gasoline and electronic injection devices in automobiles, the structure and materials of fuel hoses have changed greatly. The inner rubber layer has been replaced by fluorine rubber instead of nitrile rubber. In order to reduce fuel penetration and further improve heat resistance, the inner rubber layer has been The rubber layer mostly adopts a composite structure, which is composed of fluorine rubber and chlorohydrin rubber or acrylate rubber. Since fluorine rubber is relatively expensive, the fluorine rubber layer is relatively thin, with a thickness of about 0.2 to 0.7 mm. This kind of structure fuel hose has become a mainstream product abroad. Our country has also developed this kind of hose with fluororubber as the inner layer, and it is used in Santana, Audi, Jetta, Fukang and other models of cars. In terms of automobile engines, gearboxes, and valve oil seals with high technical content, the materials selected are mainly fluorine rubber, hydrogenated nitrile rubber, etc.
Fluorine rubber and silicone rubber composite oil seals have become the most commonly used engine crankshaft oil seals. The hydraulic system of loading and unloading trucks and the hydraulic system of large loading and unloading trucks work continuously for a long time, and the oil temperature and machine parts temperature rise rapidly. Ordinary rubber cannot meet their working requirements, and fluorine rubber products can meet various demanding requirements due to their excellent temperature resistance. technical requirements. As the automotive industry's requirements for reliability and safety continue to increase, the demand for fluororubber in the automotive industry has also shown a rapid growth trend.
In addition to automotive industry applications, fluororubber seals are used in drilling machinery, oil refining equipment, natural gas and power plant desulfurization devices. They can withstand harsh conditions such as high temperature, high pressure, oil and strong corrosive media; in chemical production, fluororubber seals Parts are used in pumps and equipment containers to seal chemical substances such as inorganic acids and organic substances. In the petroleum and chemical industries, fluorine rubber sealing products are used in mechanical seals, pumps, reactors, agitators, compressor casings, valves, various instruments and other equipment. They are usually used as packing for valve seats, valve stems, and diaphragms. and gaskets. Fluorine rubber is one of the indispensable high-performance materials for modern aviation, missiles, rockets, aerospace navigation, ships, atomic energy and other science and technology. In recent years, new fluorine rubber products have been continuously developed in the aviation and aerospace fields.
2. Main properties of fluororubber
Fluorine rubber has unique properties, and the properties of its vulcanized rubber are described below.
(1) Corrosion resistance: Fluorine rubber has the best corrosion resistance. Generally speaking, its stability against organic liquids (fuel oil, solvents, hydraulic media, etc.), concentrated acids (nitric acid, sulfuric acid, hydrochloric acid), high-concentration hydrogen peroxide and other strong oxidants is superior to other rubbers. .
(2) Swelling resistance: Fluorine rubber has a high degree of chemical stability and has the best media resistance among all elastomers currently. Type 26 fluorine rubber is resistant to petroleum-based oils, diester oils, silicone oils, silicic acid oils, inorganic acids, most organic and inorganic solvents, drugs, etc., and is only not resistant to low-molecular ketones, ethers, Ester, not resistant to amines, ammonia, hydrofluoric acid, chlorosulfonic acid, and phosphoric acid hydraulic oils. The dielectric performance of type 23 fluorine rubber is similar to that of type 26, and it is more unique. Its resistance to strong oxidizing inorganic acids such as fuming nitric acid and concentrated sulfuric acid is better than that of type 26. It can be immersed in 98% HNO3 at room temperature. 27 Its volume expansion is only 13% to 15%.
(3) Heat resistance and high temperature resistance: In terms of aging resistance, fluorine rubber is comparable to silicone rubber and better than other rubbers. Type 26 fluororubber can work at 250 ℃ for a long time and at 300 ℃ for a short time. Type 23 fluororubber still has high strength after aging at 200 ℃ × 1000 h, and can also withstand short-term high temperature of 250 ℃. The thermal decomposition temperature of tetrapropylene fluorine rubber is above 400 ℃ and can work at 230 ℃ for a long time. The performance changes of fluorine rubber at different temperatures are greater than those of silicone rubber and general-purpose butyl rubber. Its tensile strength and hardness both decrease significantly with the increase of temperature. The characteristics of the change of tensile strength are: below 150 ℃, with temperature It decreases rapidly with the increase of temperature, and decreases slowly with the increase of temperature between 150 and 260 ℃.
The high temperature resistance of fluorine rubber is the same as that of silicone rubber, and it can be said to be the best among current elastomers. 26-41 fluorine rubber can be used for long-term use at 250 ℃ and short-term use at 300 ℃; 246 fluorine rubber has better heat resistance than 26-41. The physical properties of 26-41 after air thermal aging at 300 ℃ × 100 h are equivalent to those of type 246 after hot air aging at 300 ℃ × 100 h. Its elongation at break can be maintained at about 100%, and the hardness is 90 to 95 degrees. . Type 246 maintains good elasticity after hot air aging at 350°C for 16 hours, maintains good elasticity after hot air aging at 400°C for 110 minutes, and contains spray carbon black, thermal carbon black or carbon fiber after hot air aging at 400°C for 110 minutes. The elongation of the rubber increases by about 1/2 to 1/3, and the strength decreases by about 1/2, but still maintains good elasticity. Type 23-11 fluorine rubber can be used at 200 ℃ for a long time and at 250 ℃ for a short time.
(4) Low temperature resistance: The low temperature performance of fluororubber is not good, which is due to its own chemical structure, such as the Tg of 23-11 type > 0 ℃. The low-temperature properties of fluororubber actually used are usually expressed by brittle temperature and compression cold resistance coefficient. The formula of the rubber compound and the shape of the product (such as thickness) have a greater impact on the brittleness temperature. If the amount of filler in the formula increases, the brittleness temperature will deteriorate sensitively. As the thickness of the product increases, the brittleness blending degree will also deteriorate sensitively. The low-temperature resistance of fluorine rubber generally allows it to maintain elasticity at a limit temperature of -15 to 20 ℃. As the temperature decreases, its tensile strength increases and appears strong at low temperatures. When used as seals, low temperature seal leakage problems often occur. Its brittleness temperature changes with the thickness of the sample. For example, the brittleness temperature of type 26 fluororubber is -45 ℃ when the thickness is 1.87 mm, -53 ℃ when the thickness is 0.63 mm, and -69 ℃ when the thickness is 0.25 mm. The brittleness temperature of its standard sample type 26 fluororubber is -25~-30 ℃, the brittleness temperature of type 246 fluororubber is -30~-40 ℃, and the brittleness temperature of type 23 fluororubber is -45~-60 ℃.
(5) Resistance to superheated water and steam: The stability of fluororubber against the action of hot water not only depends on the body material, but also on the combination of the rubber. For fluorine rubber, this performance mainly depends on its vulcanization system. Peroxide vulcanization systems are better than amine and bisphenol AF vulcanization systems. The performance of type 26 fluorine rubber using an amine vulcanization system is worse than that of general synthetic rubber such as ethylene-propylene rubber and butyl rubber.
(6) Compression deformation performance: Compression deformation is its key performance when fluororubber is used for sealing at high temperatures. The reason why Viton type fluororubber has been widely used is inseparable from its improvement in compression deformation. It is an important performance that must be controlled as a sealing product. The compression deformation performance of type 26 fluororubber is better than that of other fluororubbers, which is one of the reasons why it is widely used. Its compression deformation appears to be very large in the temperature range of 200 to 300 ℃. However, in the 1970s, the American DuPont Company improved it and developed a low compression deformation rubber compound (Viton E-60C), which was improved from a raw rubber variety (Viton A to Viton E-60) and a vulcanization system. The selection (from amine vulcanization to bisphenol AF vulcanization) has been improved, which makes the fluorine rubber have better compression deformation when sealed for a long time at a high temperature of 200 ℃. Under the condition of long-term storage of 149 ℃, the fluorine rubber has better The seal retention rate is the best among all types of rubber.
(7) Weathering resistance and ozone resistance: Fluorine rubber has excellent weathering resistance and ozone resistance. According to reports, the performance of VitonA developed by DuPont is still satisfactory after 10 years of natural storage, and there is no obvious cracking after 45 days in air with an ozone volume fraction of 0.01%. Type 23 fluororubber also has excellent weather aging resistance and ozone resistance.
(8) Mechanical properties: Fluorine rubber generally has high tensile strength and hardness, but poor elasticity. The general strength of type 26 fluorine rubber is between 10 and 20 MPa, the elongation at break is between 150 and 350%, and the tear resistance is between 3 and 4 kN/m. The strength of type 23 fluorine rubber is between 15.0 and 25 MPa, the elongation is between 200% and 600%, and the tear resistance is between 2 and 7 MPa. Generally, fluorine rubber has a large compression deformation at high temperatures. However, if compared under the same conditions, such as from the compression deformation of the same time at 150 ℃, both butadiene and chloroprene rubber are larger than type 26 fluorine rubber, and type 26 The compression deformation of fluorine rubber at 200 ℃ × 24 h is equivalent to the compression deformation of butadiene rubber at 150 ℃ × 24 h.
(9) Electrical properties: The electrical insulation properties of fluororubber are not very good and are only suitable for use under low frequency and low voltage. Temperature has a great influence on its electrical properties. When it rises from 24 ℃ to 184 ℃, its insulation resistance drops 35,000 times. The electrical insulation properties of type 26 fluororubber are not very good and are only suitable for low-frequency and low-voltage applications. Temperature has a great influence on its electrical properties, that is, as the temperature increases, the insulation resistance decreases significantly. Therefore, fluororubber cannot be used as an insulating material at high temperatures. The type and amount of fillers have a great influence on the electrical properties. Precipitated calcium carbonate gives the vulcanized rubber higher electrical properties, while other fillers have slightly worse electrical properties. As the amount of fillers increases, the electrical properties decrease.
(10) High vacuum resistance: Fluorine rubber has the best vacuum resistance. This is because fluororubber has a small outgassing rate and a very small amount of gas volatilization under high temperature and high vacuum conditions. Type 26 and 246 fluororubber can be used in ultra-high vacuum situations of 133×10-9 ~ 133×10-10 Pa, and are important rubber materials in spacecraft. The air permeability of fluorine rubber is the lowest among rubbers, similar to butyl rubber and nitrile rubber. The addition of fillers can reduce the air permeability of vulcanized rubber, and the effect of barium sulfate is more significant than that of medium particle thermal carbon black (MT). The gas permeability of fluororubber increases with temperature. The solubility of gas in fluororubber is relatively large, but the diffusion rate is very small, which is beneficial to application under vacuum conditions. The solubility of fluorine rubber to gas is relatively large, but the diffusion rate is relatively small, so the overall breathability is also small. According to reports, the breathability of type 26 fluororubber to oxygen, nitrogen, helium, and carbon dioxide gases at 30°C is equivalent to butyl rubber and butyl rubber, and better than chloroprene and natural rubber. In fluorine rubber, the addition of fillers fills the gaps inside the rubber, thereby reducing the air permeability of the vulcanized rubber, which is very beneficial for vacuum sealing.
(11) Flame resistance: The flame resistance of rubber depends on the halogen content in the molecular structure. The more halogen content, the better the flame resistance. Fluorine rubber can burn when in contact with flame, but will automatically extinguish after leaving the flame, so fluorine rubber is a self-extinguishing rubber.
(12) Radiation resistance: Fluorine rubber is a material that is resistant to moderate doses of radiation. The radiation effect of high-energy rays can cause cracking and structuring of fluorine rubber. The radiation resistance of fluororubber is relatively poor among elastomers. Type 26 rubber shows a cross-linking effect after radiation, and type 23 fluororubber shows a cracking effect. The performance of type 246 fluorine rubber changes drastically under normal temperature radiation in the air at a dose of 5×107 Lun. Under the condition of 1×107 Lun, the hardness increases by 1 to 3, the strength decreases by less than 20%, and the elongation decreases by 30% to 50%. Therefore, it is generally believed that type 246 fluororubber can withstand 1 × 107 liters, and the limit is 5 × 107 liters.
Hexafluoroisopropanol: a "magic molecule" hidden in life
HFIP, or hexafluoroisopropanol, is a toxic, colorless liquid with high polarity that can dissolve a variety of organic and inorganic substances. It is often used as a solvent for dissolving polyamides and esters, and is also used to analyze nylon.Basic definition and chemical properties of HFIPHexafluoroisopropanol (HFIP) is an important fluorine-containing fine chemical with a chemical formula of C3H2F6O and a molecular weight of 168.04. HFIP is a colorless, transparent liquid with high polarity that can easily dissolve a variety of organic and inorganic substances. Its boiling point is 59°C, melting point is -40°C, and density is 1.596g/mL (25°C). HFIP exhibits strong hydrogen bond donation ability and can effectively activate oxygen-containing functional groups such as carbonyl groups. At the same time, HFIP has a low pKa value (9.3), showing a certain weak acidity. At room temperature and pressure, HFIP is very stable, but it should be avoided from contact with redox chemicals to prevent other chemical reactions.Preparation method of HFIPThe preparation methods of HFIP mainly include gas phase method and liquid phase method. The gas phase method has a fast reaction speed, but the reaction temperature is high and side reactions are prone to occur. The liquid phase method is to combine hexafluoroacetone (HFA) with water to form hydrates containing different water, and then perform liquid phase catalytic hydrogenation reaction on them. This method can be carried out at a lower temperature and has a higher reaction efficiency. In the preparation process, expensive catalysts are usually used, and it is necessary to pay attention to impurities such as hydrogen fluoride and hydrogen chloride that may be contained in the raw materials to prevent catalyst poisoning.Main application areas of HFIP As a highly polar solvent, HFIP has a wide range of applications in many fields. It can be used to prepare a variety of fluorinated chemicals such as fluorinated surfactants, fluorinated emulsifiers, and fluorinated medicines. In addition, HFIP can also be used as a good solvent to improve reaction efficiency and control the stereoselectivity of products in organic synthesis. In the pharmaceutical industry, HFIP is used as an intermediate in the synthesis of the inhalation anesthetic sevoflurane. This innovative drug is highly favored by the market for its advantages such as no residue, fast anesthesia induction and awakening speed, and controllable anesthesia depth.Specific applications of HFIP in specific industriesPharmaceutical IndustryIn the pharmaceutical industry, HFIP is mainly used to synthesize the inhalation anesthetic sevoflurane. Sevoflurane is an anesthetic with excellent performance. Its advantages such as no residue, fast anesthesia induction and awakening, and controllable anesthesia depth make it widely used in clinical practice.Materials ScienceIn the field of materials science, HFIP's strong solubility makes it perform well in plastic recycling. It can effectively dissolve plastics mixed with pollutants and metal ions, and extract the purest plastics through liquid separation and solvent extraction processes. In addition, HFIP's low density, low viscosity and low surface tension make it exhibit superior solubility properties in polymerization reactions.Safety and storage considerations for HFIPHFIP is toxic and harmful to the human body, especially the respiratory system. When using it, appropriate safety measures should be taken, such as wearing appropriate protective clothing, gloves and goggles or masks to avoid direct contact. If it comes into contact with the eyes accidentally, rinse them immediately with plenty of water and seek medical advice. In terms of storage, HFIP should be stored in a cool, ventilated warehouse, and the storage temperature should not exceed 37°C. At the same time, it should avoid contact with prohibited substances such as oxidants, and keep the container sealed.Market Trend and Development Prospects of HFIPWith the advancement of science and technology and the development of industrialization, the market demand for HFIP, as an important fluorine-containing fine chemical, continues to grow. Especially in the fields of medicine and materials science, the application prospects of HFIP are very broad. At the same time, the improvement of environmental protection requirements will also promote the application of HFIP in the fields of plastic recycling. Therefore, it can be predicted that the market trend of HFIP will maintain a growth trend and show broad development prospects.Jiayuan is a professional manufacturer of hexafluoroisopropanol (HFIP) integrating R&D, production and sales. We have advanced production equipment, a complete quality inspection system and an experienced technical team. We always adhere to the business philosophy of survival by quality and development by reputation, and are committed to providing customers with high-quality, high-purity and cost-effective hexafluoroisopropanol products.Choose us, you will get:Professional technical support: We have an experienced technical team that can provide you with a full range of services such as product selection, application guidance, technical consultation, etc. to help you solve technical problems and optimize production processes.Perfect after-sales service: We promise to provide perfect after-sales service, establish customer files, conduct regular customer return visits, promptly resolve problems you encounter during use, and provide you with a safe and secure purchasing experience.We welcome new and old customers to call or write to us for consultation and purchase. We will wholeheartedly provide you with high-quality products and services!
More +
2025-04-23
Aluminum Fluoride Market Overview in 2024
Aluminum fluoride (AlF3) is a white powder mainly used as an additive in the production of primary aluminum metal. It essentially lowers the melting point of the alumina raw material and, together with cryolite, increases the conductivity of the electrolyte solution, thereby reducing power consumption. Aluminum fluoride is also used as a catalyst in organic synthesis and a raw material for synthesizing cryolite. Overall, the aluminum fluoride industry is in the mature stage, mainly a B2B business model, with relatively mild market competition and high industry entry barriers due to high technical requirements. On the upstream side, one of the important raw materials for aluminum fluoride is fluorite. Fluorite, the crystal form of calcium fluoride, is a halide mineral that crystallizes as an equiaxed cube. Fluorite is transparent in both visible and ultraviolet light when pure, but due to the presence of defects, it is often used as a multi-colored gemstone in decorative and gem applications. In addition to these modest uses, fluorite is also used to produce products made from fluorocarbons to weld steel, aluminum, and roads. In the past, fluorocarbon-based compounds were also used to make chlorofluorocarbons (CFCs). Due to the environmental restrictions of CFCs, fluorite-based HCFCs have replaced its role. China is the world's largest fluorite producing area, followed by Mexico, Mongolia, South Africa and other countries. The main domestic fluorite distribution is concentrated in Mongolia, Zhejiang, Hunan, Jiangxi and other places. Driven by demand, China's fluorite production accounts for a large proportion of the world, and the global and Chinese fluorite production has steadily increased since 2018.The reserve-to-production ratio of fluorite resources in the world and China is lower than that of rare earth and graphite. According to USGS data, Chinese fluorite has the characteristics of "low reserves and high production". China's fluorite reserves account for 13.2% of the world's total, while its production accounts for nearly 60%. The main fluorite consumption areas, such as the United States, Western Europe and Japan, have exhausted their fluorite resources and basically rely on imports.In the production of aluminum fluoride, it can be divided into dry AlF3, anhydrous AlF3, and wet AlF3 according to the preparation method. At present, the global aluminum fluoride is mainly dry aluminum fluoride and anhydrous aluminum fluoride, and wet aluminum fluoride is gradually being eliminated. In 2023, the market size of dry AlF3 has reached 63.97%, occupying an absolute dominant position. Dry AlF3 has become the first choice for various industrial applications due to its higher purity and better performance characteristics, especially in aluminum production. With excellent characteristics of consistency and efficiency in reducing energy consumption and improving electrolytic processes, dry AlF3 has become a more cost-effective and reliable choice for manufacturers. At the same time, the current aluminum fluoride production technology focuses on anhydrous aluminum chloride production technology that complies with low-carbon policies and has high resource utilization. Taking Duofuduo as an example, its innovative process "efficient utilization of low-grade fluorine silicon resources" anhydrous aluminum fluoride preparation technology can use low-grade fluorite, quartz sand, etc. as raw materials, broadening new ways to comprehensively utilize low-grade fluorine silicon resources, while also less environmental pollution. By using the anhydrous aluminum fluoride preparation technology that efficiently utilizes low-grade fluorine silicon resources, the production cost has been reduced by about RMB 1,000/ton, and the company's dominant position in the industry has been further consolidated.In terms of downstream applications, the aluminum fluoride market can be divided into aluminum industry, ceramic industry, and others. The aluminum industry segment brought in more than 90% of the market revenue and will grow at a CAGR of 1.03% during the forecast period. This huge market share is mainly attributed to the key role played by aluminum fluoride (AlF3) in aluminum production. AlF3 is essential in the electrolytic process of aluminum smelting, which can reduce the melting point of alumina and improve process efficiency and energy consumption. The widespread use of aluminum in various industries such as automotive, aerospace, construction, and packaging has driven the growing demand for aluminum across the globe, further consolidating the dominance of the aluminum industry.Global aluminum fluoride market maintains fluctuating growthAccording to data survey data, the global aluminum fluoride market size is expected to increase from US$1.683 billion in 2023 to US$1.856 billion in 2030, with a compound annual growth rate of 1.35% during 2024-2030. The overall growth of the aluminum industry itself directly increases the demand for aluminum fluoride, which is a key agent in the aluminum smelting process. Secondly, the demand for lightweight materials in various industries, especially automotive and aerospace, is increasing, and the use of aluminum is also increasing due to its strength and light weight. Urbanization and infrastructure development, especially in emerging economies, are pushing up the demand for aluminum in construction, further driving the development of the aluminum fluoride market. Finally, the technology of aluminum fluoride products continues to make breakthroughs, and the improvement of product performance has expanded the application field. In terms of the application of aluminum fluoride in the field of new energy, the application of aluminum fluoride products in new energy fields such as new energy vehicles, wind energy, and solar energy is increasing. In the production process of solar cells, aluminum fluoride has a low melting point and good thermal stability, which can promote the melting and mixing of solar cell materials at a lower temperature, reduce the lattice defects of solar cells, increase carrier mobility, and thus improve the conversion efficiency of solar cells.On the other hand, the future growth of the electrolytic aluminum industry is limited. The electrolytic aluminum production capacity of major industrial countries in the world is close to the limit. For example, as of June 2023, China's electrolytic aluminum production capacity has reached 44.711 million tons, and the operating capacity is 41.648 million tons, an increase of 1.85% year-on-year and 1.38% month-on-month, which is gradually approaching the production capacity limit. At the same time, electrolytic aluminum is a high-energy-consuming variety, which is inconsistent with the important strategy of global low-carbon transformation. The growth of the electrolytic aluminum industry will also be restricted by low-carbon policies.Industry competition landscapeFrom the perspective of industry competition, according to data, the market concentration indexes CR5 and HHI of the global aluminum fluoride market will reach 40.62% and 4.11% respectively in 2023. This shows that the top companies control the market to a certain extent, but the market still maintains a fierce competitive environment, and smaller players also have opportunities. The leading companies in the market are mainly in China, contributing most of the production capacity and sales.Changzhou Jiayuan Chemical Co., Ltd. is a high-tech enterprise specializing in the research and development, production and sales of aluminum fluoride. The company has advanced production equipment and a complete quality management system. The product quality is stable and reliable, and is deeply trusted by domestic and foreign customers.The aluminum fluoride produced by our company has the following advantages:High purity: The main content is as high as 99.95 %, and the impurity content is low, meeting the needs of different application fields.Uniform particle size: Using advanced crushing and grading technology, the product particle size distribution is uniform and has good fluidity.Stable quality: Strictly control every link in the production process to ensure stable and reliable product quality.Favorable price: Large-scale production has obvious cost advantages and provides customers with cost-effective products.Thoughtful service: Provide comprehensive technical support and after-sales service to resolve customers' worries.
More +
2025-04-23
Industrial lithium carbonate and battery grade lithium carbonate
Summary:1. Definition and difference between industrial lithium carbonate and battery grade lithium carbonate2. Process improvement for upgrading industrial lithium carbonate to battery-grade lithium carbonate3. Progress of upgrading industrial lithium carbonate to battery-grade lithium carbonate4. Market demand and price differences between industrial lithium carbonate and battery-grade lithium carbonateText :1. Definition and difference between industrial lithium carbonate and battery-grade lithium carbonateIndustrial lithium carbonate and battery-grade lithium carbonate are both types of lithium carbonate, and the main difference lies in their purity. The purity of industrial lithium carbonate is higher, reaching 98%-99%, while the purity requirement of battery-grade lithium carbonate is higher, not less than 99.5%. Due to the high purity requirement, battery-grade lithium carbonate is usually used in fields such as lithium battery manufacturing.2. Process improvement of upgrading industrial lithium carbonate to battery-grade lithium carbonateThe process improvement of upgrading industrial lithium carbonate to battery-grade lithium carbonate mainly includes purification process and production process. The purification process mainly improves the purity of lithium carbonate through lithium precipitation, filtration and other methods. The production process requires controlling temperature, pressure and other conditions to ensure product quality. 3. Progress of upgrading industrial lithium carbonate to battery-grade lithium carbonateChina is promoting the process improvement of upgrading industrial lithium carbonate to battery-grade lithium carbonate. At present, the commissioning of battery-grade lithium carbonate equipment and the construction of lithium sinking equipment are progressing smoothly and will all be put into operation by the end of 2024.4. Market demand and price difference between industrial lithium carbonate and battery-grade lithium carbonateIn recent years, with the rapid development of industries such as electric vehicles, the demand for battery-grade lithium carbonate has continued to increase. At the same time, due to the complexity and high cost of the production process of battery-grade lithium carbonate, its market price is also higher than that of industrial lithium carbonate.In summary, the process improvement of upgrading industrial lithium carbonate to battery-grade lithium carbonate is gradually making progress, and the market demand for battery-grade lithium carbonate will continue to grow in the future.In the field of new energy materials, the performance indicators of battery-grade lithium carbonate determine the quality of many products. Our company focuses on the research and development and production of battery-grade lithium carbonate. We have industry-leading technology and equipment, and the indicators of the battery-grade lithium carbonate we produce have reached the international advanced level. Here, with a professional attitude, we welcome you to order battery-grade lithium carbonate from our company and open a new chapter in the application of high-efficiency battery materials.
More +
2025-03-28
Analysis of the current status of the hexafluoropropylene industry in 2024
1. Introduction and application of hexafluoropropyleneHexafluoropropylene oligomers, also known as perfluoroolefin oligomers, are mixed oligomers prepared from hexafluoropropylene, mainly including hexafluoropropylene dimer (HFPD) and hexafluoropropylene trimer (HFPT). From the perspective of upstream raw materials, hexafluoropropylene (HFP), also known as perfluoropropylene, is an organic compound, and its preparation methods include the thermal decomposition of difluorochloromethane and the thermal decomposition of tetrafluoroethylene. Hexafluoropropylene has a wide range of applications and the market demand is growing. In 2023, the market demand in China will reach about 70,000 tons.Hexafluoropropylene dimer (HFPD) is a compound obtained by oligomerization of two hexafluoropropylene molecules under the action of a catalyst. Due to the presence of carbon-fluorine bonds in its molecular structure, hexafluoropropylene dimer has the characteristics of strong heat resistance, high chemical stability, water-repellent, oil-repellent, and antifouling. Based on this, hexafluoropropylene dimer can be used to make fluorinated surfactants (such as wetting agents, emulsifiers, penetrants), fluorinated cleaning agents, etc. Hexafluoropropylene trimer (HFPT), also known as perfluorononene, is obtained by trimerization of hexafluoropropylene gas. Hexafluoropropylene trimer has three isomers, namely perfluoro-2,4-dimethyl-3-heptene (T-1), perfluoro-4-methyl-3-isopropyl-2-pentene (T-2), and perfluoro-2,4-dimethyl-3-ethyl-2-pentene (T-3). Hexafluoropropylene trimer is an environmentally friendly solvent and can be used as a desiccant, cleaning agent, diluent, etc. 2. Scale and development history of hexafluoropropylene trimer industry2.1 Industry BackgroundHexafluoropropylene trimer (HFP Trimer) is an important fluorine-containing fine chemical, widely used in electronics, medicine, coatings and high-performance materials. With the rapid development of China's economy and technological progress, the demand for hexafluoropropylene trimer has increased year by year, and the market size has continued to expand.2.2 Historical DevelopmentSince 2010, China's hexafluoropropylene trimer industry has experienced a rapid development stage. In 2010, the market size of hexafluoropropylene trimer in China was only RMB 250 million, and the output was about 1,500 tons. With the expansion of downstream application fields and the improvement of technical level, market demand has gradually increased. In 2015, the market size grew to RMB 680 million and the output reached 4,000 tons. Entering 2020, despite the impact of the global COVID-19 pandemic, China's hexafluoropropylene trimer industry has maintained a steady growth trend. In 2020, the market size reached RMB 1.23 billion and the output was 7,500 tons. This growth is mainly due to the strong demand in the electronics industry and high-performance materials market, especially the development of new energy vehicles and 5G communication technology, which further promoted the application of hexafluoropropylene trimer.2.3 Current SituationIn 2024 , the market size of China's hexafluoropropylene trimer industry further expanded to RMB 1.85 billion, and the output exceeded 10,000 tons. This growth was mainly due to the following aspects:2.3.1 Expansion of downstream application areasWith the rapid development of high-tech industries such as new energy vehicles, 5G communications, and semiconductor manufacturing, the demand for hexafluoropropylene trimer continues to increase.2.3.2 Technological innovationDomestic enterprises have made remarkable progress in production processes and technology research and development, improving product quality and production efficiency.2.3.3 Policy supportThe Chinese government has introduced a series of support policies to encourage the development of new materials and high-end manufacturing industries, providing a good external environment for the hexafluoropropylene trimer industry.2.4 Future predictionsIt is estimated that by 2025, the market size of China's hexafluoropropylene trimer industry will reach RMB 2.68 billion, and the output is expected to reach 14,000 tons. This forecast is based on the following considerations:2.4. 1. Market demand continues to growWith the further development of new energy vehicles, 5G communications, semiconductor manufacturing and other fields, the demand for hexafluoropropylene trimer will continue to increase.2.4.2 Technological progressDomestic companies will continue to increase investment in research and development, improve product quality and production efficiency, and enhance market competitiveness.2.4.3. Policy supportThe government will continue to introduce relevant policies to support the development of new materials and high-end manufacturing industries and provide strong policy guarantees for the hexafluoropropylene trimer industry.2.5 Hexafluoropropylene trimer market characteristics and competition landscape2.5.1 Market CharacteristicsChina's hexafluoropropylene trimer (HFP) industry has developed rapidly in recent years, and the market size continues to expand.In 2018, the total output of China's HFP market reached about 15,000 tons, an increase of 8% year-on-year. This growth was mainly due to the rapid development of downstream application fields, especially the increase in demand in the fields of electronic chemicals, pharmaceutical intermediates and high-performance materials.2.5.2 Demand driversElectronic chemicals : With the rapid development of industries such as 5G communications, semiconductors and new energy vehicles, the demand for electronic chemicals has increased significantly. In 2023, the demand for HFP in the electronic chemicals field will reach 40%, and it is expected to further increase to 45% by 2025.Pharmaceutical intermediates : HFP is also increasingly used in pharmaceutical intermediates, especially in the research and development of new drugs. In 2023, the demand for HFP in the pharmaceutical intermediates field will account for about 25%, and it is expected to reach 30% by 2025.High-performance materials : The application of HFP in high-performance materials, such as specialty rubbers and coatings, is also showing good growth. In 2023, the demand for HFP in the high-performance materials field will account for about 35%, and it is expected to reach 37% by 2025.Hexafluoropropylene is mainly used to synthesize fluoropolymers, such as fluororubber and fluororesin, which have excellent performance in high temperature and chemical corrosion environments. With the continuous expansion of downstream markets , the market demand for hexafluoropropylene is also showing a steady growth trend.3. Current status of hexafluoropropylene industryHexafluoropropylene is one of the important fluorine-containing polymer materials, with a wide range of downstream applications and a growing market demand. In recent years, China's hexafluoropropylene production capacity and output have expanded significantly. In recent years, the global and Chinese hexafluoropropylene market has continued to expand. The hexafluoropropylene report shows that China's hexafluoropropylene production will be about 83,000 tons in 2022. With the continuous advancement and innovation of production technology, the production efficiency and product quality of hexafluoropropylene will continue to improve. This will help reduce production costs and improve market competitiveness.There are many hexafluoropropylene manufacturers and the market competition is fierce. Most of China's hexafluoropropylene manufacturers are large fluorine chemical companies , and Jiayuan follows closely. With the rapid development of downstream industries, China's HFP production capacity and output scale have expanded significantly in recent years. In 2024, China's hexafluoropropylene production will exceed 83,000 tons, and market demand will maintain a growth trend. The global and Chinese hexafluoropropylene market scale continues to expand, and the total effective market production capacity has reached 115,600 tons/year .the main producers of hexafluoropropylene include DuPont, 3M, and Daikin Industries, Ltd. In China, hexafluoropropylene manufacturers including Jiayuan have a certain production scale and market share. With the improvement and innovation of technology, the production efficiency and product quality of hexafluoropropylene are constantly improving.4. Production technology level of hexafluoropropylene industry Hexafluoropropylene is mainly produced by chemical reactions such as cracking of tetrafluoroethylene (TFE), decarboxylation of perfluorocarboxylic acid or perfluorocarboxylate. Among them, cracking of tetrafluoroethylene is the most important production process. In addition, hexafluoropropylene is produced by direct cracking of R22, thermal decomposition of perfluorocyclobutane and its isomers, etc., but these methods are rarely used in industry.The reaction process of tetrafluoroethylene cracking to produce hexafluoropropylene is complex and involves multiple side reactions. It requires precise control of reaction conditions and catalysts to improve the yield and purity of hexafluoropropylene. The cracking reaction is carried out under high temperature and high pressure, and has extremely high requirements on equipment materials and sealing performance to prevent reactant leakage and safety accidents. The cracking reaction is an endothermic reaction that consumes a lot of heat energy, and the by-products produced during the reaction also need to be subsequently processed, which increases energy consumption and costs. The current status analysis of the hexafluoropropylene industry mentioned the development of new high-efficiency catalysts to improve the activity and selectivity of tetrafluoroethylene cracking reactions and reduce the occurrence of side reactions, thereby increasing the yield and purity of hexafluoropropylene. Reaction condition optimization optimizes the cracking reaction process by precisely controlling reaction temperature, pressure, residence time and other conditions, reducing energy consumption and the generation of by-products. Comprehensively utilize the by-products produced by the cracking reaction, such as further processing by-products such as octafluorocyclobutane into other valuable chemicals, to improve resource utilization and economic benefits.V. ConclusionIn summary, the production process level of hexafluoropropylene industry is constantly improving, but it still needs further optimization and innovation. Driven by factors such as technological innovation, industrial integration and market demand growth, Jiayuan hexafluoropropylene industry will usher in a broader development prospect.Dear customers and friends, when you are looking for high-quality hexafluoropropylene products in the dazzling market, we sincerely welcome you to choose our company for ordering. Our company has been deeply involved in the fluorine chemical industry for many years, and has accumulated rich experience and strong strength. It has a professional R&D team to ensure that each product is carefully polished and has excellent quality and outstanding performance. Whether it is product quality, logistics , or after-sales service, we strive to be perfect . During the Spring Festival, considering the particularity of logistics and other aspects, we have comprehensively optimized and adjusted the delivery process. We communicated and coordinated closely with logistics partners in advance and formulated a delivery plan for special periods to ensure that your goods can be delivered safely and in time. Although the delivery during the Spring Festival is different from usual, our pursuit of perfection has never changed. Whether it is product quality control, accurate presentation of functions, or the intimacy of after-sales service, we go all out to achieve perfection.We always put customer satisfaction first and cherish every choice you make. So, when you need hexafluoropropylene, please do not hesitate and welcome to order from our company. Believe us, we will not let you down during this Spring Festival and will definitely bring you a quality experience beyond your imagination.
More +
2025-03-28